By dk-tester | 30 January 2024 | 0 Comments
Maximize Efficiency: Optimizing Li-ion Battery Testing Workflows
The demand for lithium-ion batteries (Li-ion) is skyrocketing as industries shift towards electrification. Consequently, there has been an upsurge in Li-ion battery testing to ensure their reliability, safety, and efficiency. Battery testing equipment plays a significant role in Li-ion battery testing workflows. As testing volumes increase, there is a need for efficient and optimized processes to increase productivity and ensure consistent results. In this blog, we explore how to leverage data analytics, customize testing equipment, and overcome challenges in high-volume testing operations to maximize efficiency.
Streamlining Testing Processes for Enhanced Productivity:
The fundamental principle of testing is to ensure that the resulting product meets the required standards. Achieving this requires careful optimization of the testing process, with emphasis on speed, repeatability, and quality. An efficient testing process is one where each step flows seamlessly into the next without bottlenecks or delays. Automating repetitive and time-consuming tasks such as data entry, reporting, and analysis can significantly improve productivity. An integrated software solution that streamlines these processes can reduce testing time and frees up resources. Choosing the right Li-ion testing equipment, such as charge/discharge systems that can be controlled remotely from the operating console, can also save significant time.
Leveraging Data Analytics for Insightful Battery Testing:
Data analytics has revolutionized how businesses operate, and battery testing is no exception. With the increasing complexity of Li-ion batteries, it's no longer enough to rely on manual analysis of data. Analytics tools enable real-time processing and analysis of vast amounts of data generated during battery testing. Predictive analytics, for example, can detect patterns and trigger alerts for maintenance issues before they occur, resulting in fewer failures and downtime. Analytics tools can also generate insights, such as identifying cell-to-cell variability in battery packs. These insights enable better design and optimization of battery manufacturing processes and materials.
Customizing Testing Equipment for Specific Li-ion Battery Applications:
The flexibility to customize testing equipment to specific Li-ion battery applications is essential for obtaining accurate results. Customizations could include modifying the equipment to handle different voltages and currents or to match the size and shape of the battery being tested. More advanced customization may add features such as automatic temperature monitoring or integrating with other testing equipment. A bespoke solution may cost more upfront, but the potential long-term benefits to efficiency, accuracy, and productivity make it worthwhile.
Overcoming Challenges in High-Volume Battery Testing Operations:
High-volume battery testing operations can pose unique challenges related to staffing, equipment malfunctions, fatigue, and safety. Human error can creep into high-stress environments, and meticulous attention to detail is essential. The first step to avoiding these errors is to have a robust testing process, clearly defined protocols, and adequate staffing. Ensuring equipment reliability can help minimize downtime, delays, and disruptions. Regular maintenance and calibration of testing equipment are crucial for precise results and preventing safety incidents.
The Importance of Maintenance and Calibration in Battery Testing Equipment:
To deliver consistent and reliable testing results, Li-ion battery testing equipment must be calibrated and maintained regularly. The calibration process removes any drift or variation from the equipment, ensuring accurate readings. Maintenance tasks such as cleaning, lubrication, and replacing parts prevent wear and tear, extend machine life and reduce equipment downtime. Regular equipment checks, including inspection, functional tests and adjustment, also reduce the risk of damage to the battery being tested or the equipment itself.
The optimal testing workflow is one that maximizes efficiency while ensuring accuracy and reliability. Battery testing equipment is a critical component of the process that demands attention to detail. Streamlining testing processes, leveraging data analytics, customizing testing equipment, overcoming high-volume testing challenges, and maintaining testing equipment are essential to maximizing efficiency. Achieving this requires investing in the right equipment and personnel, implementing standardized protocols, and prioritizing safety. By optimizing Li-ion battery testing workflows, companies can continue to drive down costs, increase productivity, and meet the ever-growing demands for reliable Li-ion battery technologies.
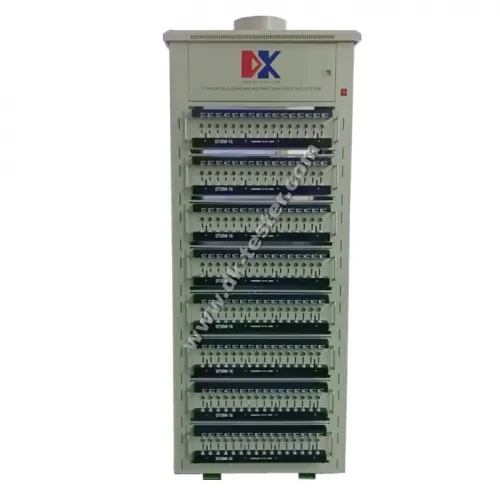
Streamlining Testing Processes for Enhanced Productivity:
The fundamental principle of testing is to ensure that the resulting product meets the required standards. Achieving this requires careful optimization of the testing process, with emphasis on speed, repeatability, and quality. An efficient testing process is one where each step flows seamlessly into the next without bottlenecks or delays. Automating repetitive and time-consuming tasks such as data entry, reporting, and analysis can significantly improve productivity. An integrated software solution that streamlines these processes can reduce testing time and frees up resources. Choosing the right Li-ion testing equipment, such as charge/discharge systems that can be controlled remotely from the operating console, can also save significant time.
Leveraging Data Analytics for Insightful Battery Testing:
Data analytics has revolutionized how businesses operate, and battery testing is no exception. With the increasing complexity of Li-ion batteries, it's no longer enough to rely on manual analysis of data. Analytics tools enable real-time processing and analysis of vast amounts of data generated during battery testing. Predictive analytics, for example, can detect patterns and trigger alerts for maintenance issues before they occur, resulting in fewer failures and downtime. Analytics tools can also generate insights, such as identifying cell-to-cell variability in battery packs. These insights enable better design and optimization of battery manufacturing processes and materials.
Customizing Testing Equipment for Specific Li-ion Battery Applications:
The flexibility to customize testing equipment to specific Li-ion battery applications is essential for obtaining accurate results. Customizations could include modifying the equipment to handle different voltages and currents or to match the size and shape of the battery being tested. More advanced customization may add features such as automatic temperature monitoring or integrating with other testing equipment. A bespoke solution may cost more upfront, but the potential long-term benefits to efficiency, accuracy, and productivity make it worthwhile.
Overcoming Challenges in High-Volume Battery Testing Operations:
High-volume battery testing operations can pose unique challenges related to staffing, equipment malfunctions, fatigue, and safety. Human error can creep into high-stress environments, and meticulous attention to detail is essential. The first step to avoiding these errors is to have a robust testing process, clearly defined protocols, and adequate staffing. Ensuring equipment reliability can help minimize downtime, delays, and disruptions. Regular maintenance and calibration of testing equipment are crucial for precise results and preventing safety incidents.
The Importance of Maintenance and Calibration in Battery Testing Equipment:
To deliver consistent and reliable testing results, Li-ion battery testing equipment must be calibrated and maintained regularly. The calibration process removes any drift or variation from the equipment, ensuring accurate readings. Maintenance tasks such as cleaning, lubrication, and replacing parts prevent wear and tear, extend machine life and reduce equipment downtime. Regular equipment checks, including inspection, functional tests and adjustment, also reduce the risk of damage to the battery being tested or the equipment itself.
The optimal testing workflow is one that maximizes efficiency while ensuring accuracy and reliability. Battery testing equipment is a critical component of the process that demands attention to detail. Streamlining testing processes, leveraging data analytics, customizing testing equipment, overcoming high-volume testing challenges, and maintaining testing equipment are essential to maximizing efficiency. Achieving this requires investing in the right equipment and personnel, implementing standardized protocols, and prioritizing safety. By optimizing Li-ion battery testing workflows, companies can continue to drive down costs, increase productivity, and meet the ever-growing demands for reliable Li-ion battery technologies.
Leave a Reply
Your email address will not be published.Required fields are marked. *
POPULAR BLOG
- Advanced Battery Testing: Key to Efficient EV Manufacturing and Market Success
- Empowering Industries: Applications of Li-ion Battery Testing Equipment
- Maximize Your Electric Car's Performance with Our Battery Tester
- Advancing Electric Vehicle Performance with Lithium Battery Testing
- 5V 50A Electric Car Lithium Battery Charge Discharge Testing and Balance Repair Machine
CATEGORIES